Get reliable results with expert plastic extrusion techniques
Get reliable results with expert plastic extrusion techniques
Blog Article
Secret Advantages and Factors To Consider of Applying Plastic Extrusion in Your Jobs

Recognizing the Essentials of Plastic Extrusion
Plastic extrusion, a staple in the production market, is a process that includes melting raw plastic material and improving it right into a continuous profile. This account, when cooled, can be cut into desired sizes or coiled for later use. The beauty of plastic extrusion hinges on its convenience. A vast array of items, from piping to window frames, can be generated. The process needs an extruder, a complex device with a warmed barrel, a revolving screw, and a die at the end. The plastic material, in the type of pellets, is fed right into the extruder, where it's thawed and forced through the die, taking its form. The choice of plastic and the layout of the die determine the item's features.
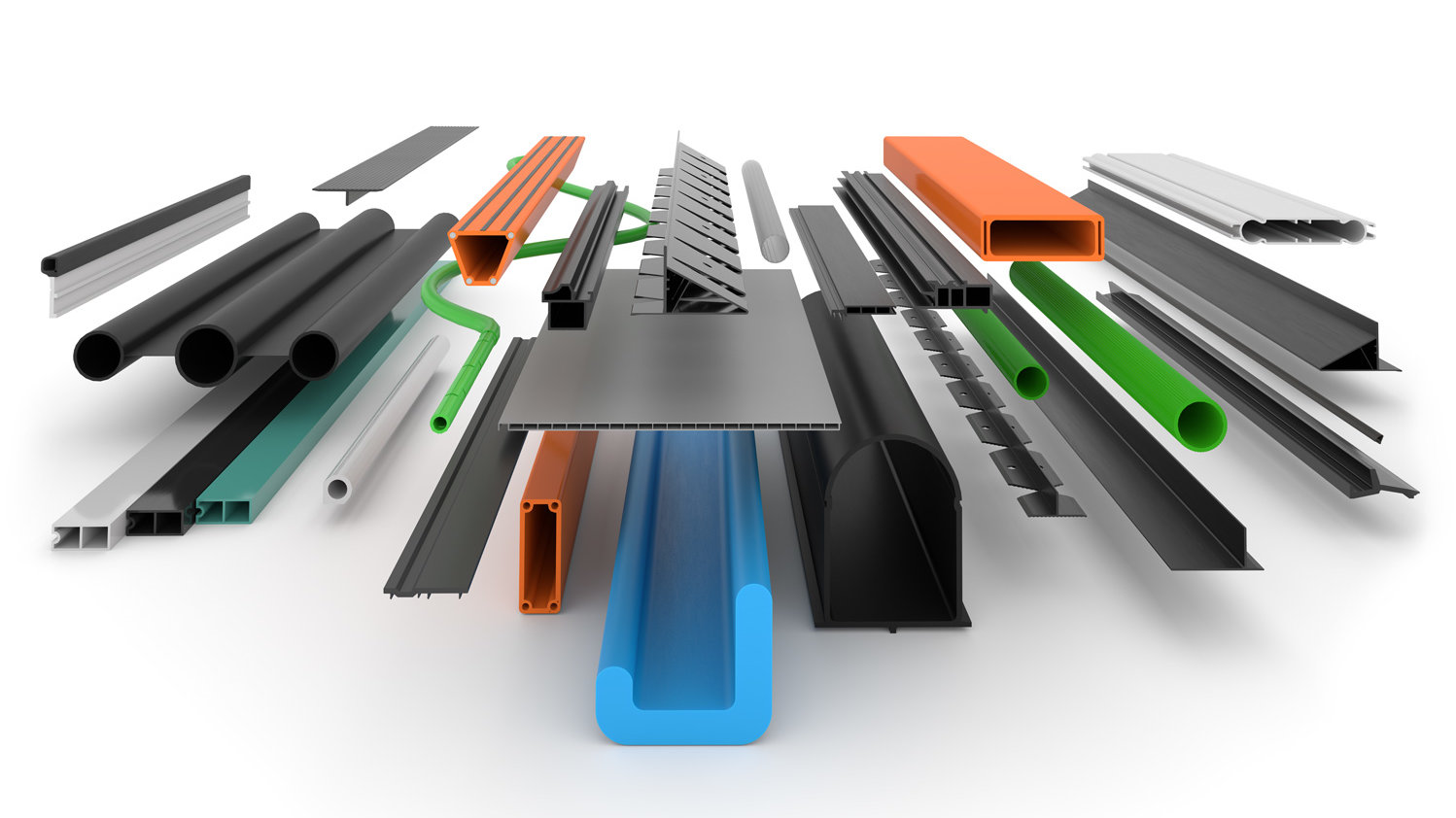
The Economic Advantage of Plastic Extrusion
The economic advantage of plastic extrusion exists predominantly in 2 locations: cost-effective material manufacturing and advantageous production speeds. With plastic extrusion, businesses can create high quantities of product at a lower expense contrasted to other techniques. The process boasts an excellent manufacturing rate, dramatically decreasing time and additional boosting its financial viability.
Cost-Effective Material Manufacturing
A substantial advantage of plastic extrusion is its impressive cost-effectiveness. This production process permits constant, high-volume production with marginal waste, which translates right into lower expenses. The raw materials made use of, commonly plastic pellets, are reasonably economical contrasted to other compounds (plastic extrusion). The process itself calls for much less power than lots of various other production methods, even more decreasing expenses. In addition, the extrusion process enables a high level of accuracy in forming the plastic, minimizing the need for pricey post-production alterations or adjustments. The toughness and durability of extruded plastic products usually suggest less require for substitutes, contributing to lasting financial savings. All these factors make plastic extrusion a very cost-effective choice for several projects, using an attractive equilibrium in between price and efficiency.
Beneficial Production Speeds
While maintaining the cost-effectiveness of the products, another notable benefit of plastic extrusion lies in its rapid production rates. This efficiency in the manufacturing process is attributed to the constant nature of the extrusion procedure, permitting high-volume production in a relatively brief time period. The speed of production straight correlates to a decrease in labor expenses and a rise in output, thus boosting the total economic stability of the process. The fast-paced production does not compromise the quality of the final product, making sure regular and reputable outcomes. This mix of high quality, speed, and cost-effectiveness emphasizes the significant economic benefit of implementing plastic extrusion in various jobs.
Convenience and Personalization: The Toughness of Plastic Extrusion
Among the prominent toughness of plastic extrusion exists in its convenience and customization possibility. These top qualities open the door to limitless layout opportunities, offering producers the ability to customize products to particular needs. This enhanced level of modification not only improves item performance but additionally dramatically enhances product originality.
Unrestricted Design Possibilities
Plastic extrusion beams in its capacity to offer almost endless style possibilities. Plastic extrusion can deal with a range of plastic types, increasing its application extent. With plastic extrusion, the design possibilities are essentially limitless.
Boosting Item Originality
The flexibility of plastic extrusion can significantly enhance product uniqueness. This process allows developers to More Bonuses explore various shapes, sizes, and shades, offering them the flexibility to produce distinct products that stand apart in the marketplace. It is this modification that provides an unique identity to every item, identifying it from its rivals.
In addition to its aesthetic advantages, the customizability of plastic extrusion likewise supplies functional benefits. Designers can customize the residential or commercial properties of the plastic according to the particular demands of the application, boosting the item's performance. For example, they can make the plastic more adaptable, a lot more resilient, or much more resistant to warmth, depending upon what the item calls for. Thus, plastic extrusion not just increases product originality yet also its energy and bankability.
Layout Limitations in Plastic Extrusion: What You Need to Know
Just how can develop constraints potentially affect the procedure of plastic extrusion? While plastic extrusion is versatile, layout restrictions can stop its advantages. Particular complex styles might not be viable because of the constraints of the extrusion process, potentially limiting the development of detailed profiles. The procedure is much less ideal for multi-chambered or hollow structures. Furthermore, the extrusion procedure might not always offer the desired surface finish, especially for those needing high gloss or optical clarity. Material choice can likewise present challenges, as not all polymers appropriate for extrusion. High-temperature immune plastics, for example, may provide troubles. Understanding these restrictions is critical for effective implementation of plastic extrusion in your jobs. plastic extrusion.
Evaluating the Environmental Impact of Plastic Extrusion
While comprehending design limitations is a considerable facet of get redirected here plastic extrusion, it is just as vital to consider its ecological ramifications. The process of plastic extrusion includes melting plastic products, potentially releasing hazardous gases into the atmosphere. Even more, the resulting products are often non-biodegradable, adding to land fill waste. Advancements in modern technology have actually enabled for more environmentally-friendly techniques. As an example, utilizing recycled plastic products in the extrusion procedure can minimize environmental effect. Furthermore, developing naturally degradable plastic choices can aid minimize waste problems. Assessing these ecological aspects is crucial when implementing plastic extrusion tasks, making sure a balance in between performance, cost-effectiveness, and environmental duty.
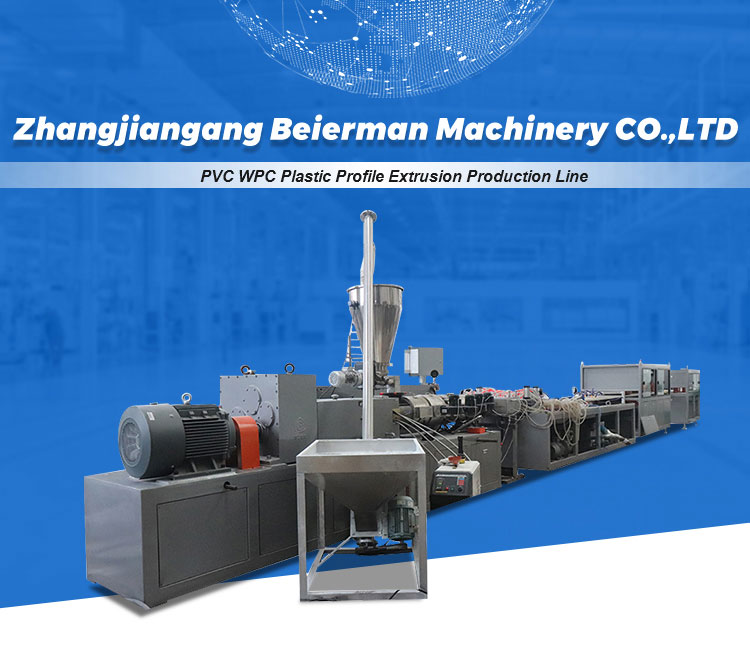
Study: Successful Projects Utilizing Plastic Extrusion
Success tales in the area of plastic extrusion are plentiful, demonstrating both the flexibility and effectiveness of this production process. plastic extrusion. An additional effective case is the manufacturing of plastic film for packaging and farming. These circumstances highlight plastic extrusion's critical function in various fields, confirming to its adaptability, cost-effectiveness, and dependable result.
Final thought
In final thought, plastic extrusion uses a reliable and affordable method for creating intricate shapes with marginal waste. Including plastic extrusion right into tasks can lead to effective outcomes, as confirmed by many situation researches.
Plastic extrusion, a staple in the manufacturing industry, is a process that includes melting raw plastic product and improving it into a constant profile. Plastic the original source extrusion can manage a selection of plastic kinds, expanding its application range.Just how can make constraints potentially affect the procedure of plastic extrusion? The process of plastic extrusion includes melting plastic materials, potentially releasing hazardous gases right into the environment. Making use of recycled plastic products in the extrusion procedure can decrease environmental impact.
Report this page